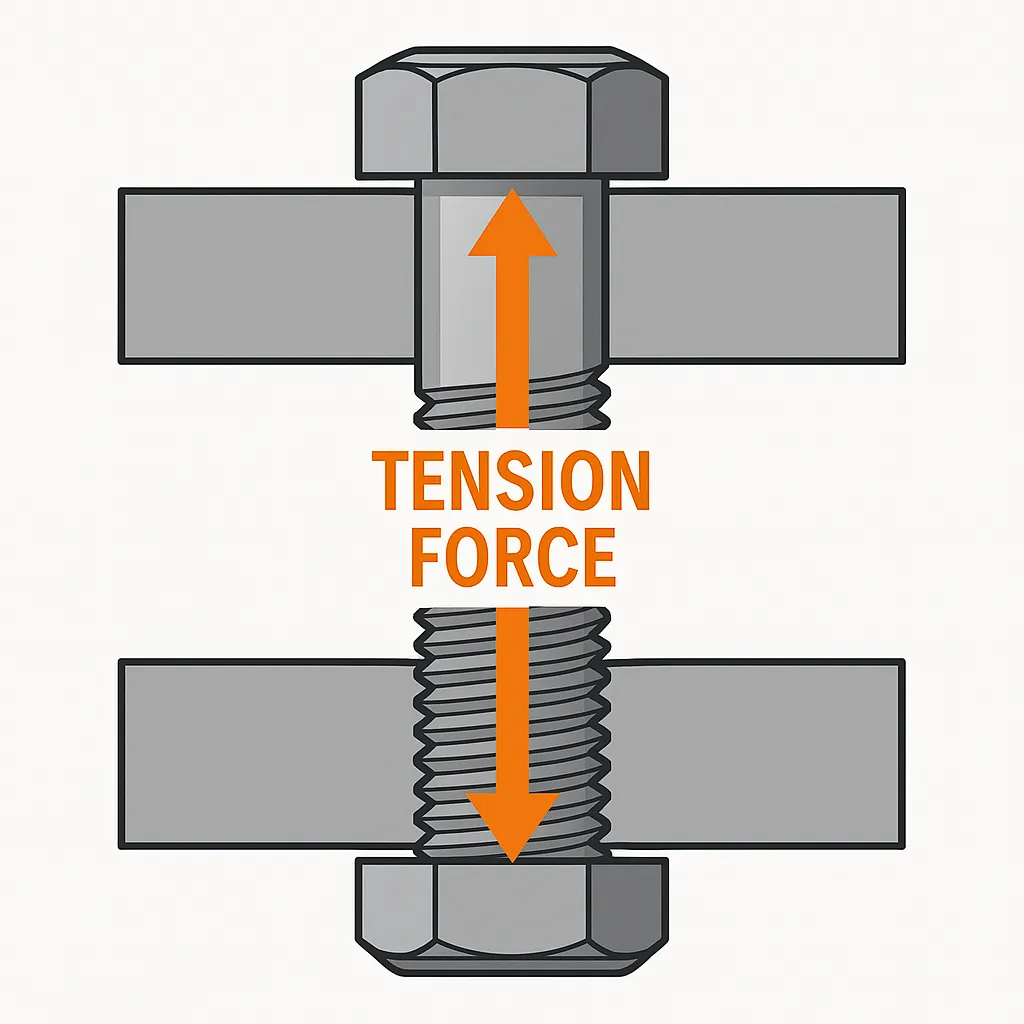
軸力
軸力とはボルトを締め付けたときにボルト軸方向(縦方向)に発生する引っ張りの力のことを指します。これはボルトナットの確実な締付けや接合部の信頼性を保つうえで重要な概念です。具体的に言うとボルトで部材同士を締結するとき、ナットを回してボルトを引っ張ることでボルトはバネのように伸びた状態(わずかな伸び)になります。このとき、ボルトは常に元に戻ろうとする力、つまり「引っ張り力(軸力)」を発生させます。そしてこの軸力によって、接合面が強く押し合わされ、すき間なく密着することで、緩みやズレを防ぎ、確実な締結状態が得られるのです。
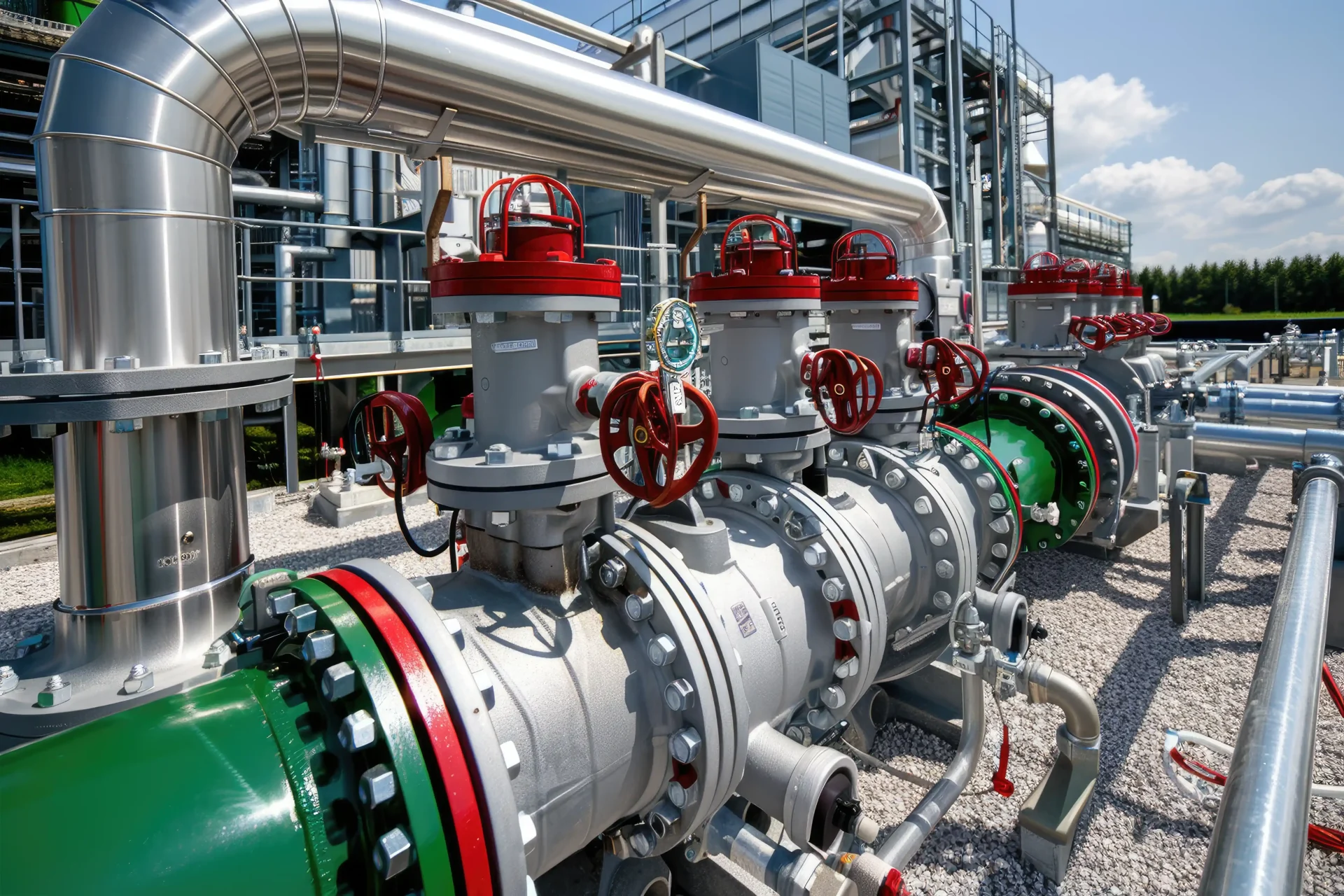
フランジ接合部のボルト
たとえば、配管のフランジ接合部などでは、ガスや液体が漏れないようにするためにガスケット(パッキン)を強く圧縮する必要があります。その圧縮力を生み出しているのがボルトの軸力です。逆に軸力が不足していると接合面にすき間が生じ、振動や内圧によりナットが緩んだり、漏れが発生したりする危険性があります。
タワートップボルトにおける締付トルクと導入軸力の関係について
https://windeng.t.u-tokyo.ac.jp/ishihara/presentation/2015-27.pdf
締め付けのトルクと軸力を調整する際の注意点は?
締め付けのトルクと軸力を調整する際にはいくつかの重要な注意点があります。まず、最も大きなポイントは「トルクをかけること=軸力が正確に得られる」というわけではないという点です。実際にはトルクの大部分はねじ山や座面との摩擦に使われており、残りの一部だけがボルトを引っ張る「軸力」として作用します。そのため摩擦条件が変われば同じトルクをかけても得られる軸力は大きく変動することになります。
例えば、潤滑剤を塗布した場合と乾いた状態で締めた場合では摩擦係数が異なるため、同じトルクでも軸力に大きな違いが生まれます。したがって、トルク値を設定する際には必ず前提となる摩擦条件(潤滑の有無、表面処理の種類など)を確認し、それに合わせて適切な値を選定しなければなりません。
また、使用するトルクレンチや油圧トルクレンチなどの工具が正しいトルクを発生させているかどうかも重要です。これらの工具は使い続けることで精度のばらつきが拡大するため、定期的に校正や点検を行う必要があります。特に重要な締結部位には校正して間もない工具を使うことです。
さらにボルトやナットの状態にも注意が必要です。錆びついていたり、傷がついていたりするボルトナットは摩擦が増加し、適切な軸力が得られない原因となります。こうした状態のボルトナットは再使用せず、新品と交換することが望ましいです。
加えて、複数のボルトを締める際にはその順序や回数にも注意を払うべきです。例えばフランジのような接合部では、均等に締め付けなければ一部のボルトだけに過剰な負荷がかかり、軸力がばらついてしまいます。一般的には対角線状に順番を変えながら、3段階ほどに分けて段階的に締める方法が推奨されます。
軸力管理の重要性について
軸力管理の重要性はボルト締結が構造物や機械の安全性・耐久性・機能性を左右する根幹であるという点にあります。ボルトを締める目的は単に部品同士をくっつけることではなく、「必要な軸力(ボルトを引っ張る力)を正確に加えること」によって、すき間をなくし、緩みや漏れ、破損を防止するためです。
具体的に言うとたとえば配管フランジの接合部では内部の圧力でガスや液体が漏れないよう、ガスケットをしっかり圧縮する必要があります。この圧縮力を生み出しているのが、ボルトの軸力です。軸力が足りなければガスケットが密着せず、漏れの原因になります。逆に、軸力が強すぎるとガスケットを押しつぶしすぎて破損させたり、ボルト自体が塑性変形して締結力を失ってしまうこともあります。
また、橋梁や鉄塔などの構造物でも軸力は非常に重要です。風や地震による振動を受けたとき、ボルトの軸力が適切に管理されていないと接合部にゆるみが発生し、最終的には部材のズレや脱落につながるおそれがあります。実際に過去の建設事故の中には、締付けトルクや軸力の管理不足によって大きな損害が出た事例も存在します。
さらにボルトが複数本ある場合、それぞれのボルトに均等な軸力を加えることが極めて重要です。一本だけ軸力が高かったり、低かったりすると、荷重が不均一にかかって構造が歪んだり、一部のボルトに過負荷が集中して破断を招くことがあります。軸力を適切に管理することで、全体のバランスを保ち、構造の長期的な安定を確保することができるのです。
このように、ボルト締結という一見単純に見える作業でも、「軸力」という見えない力の管理が、設備の信頼性と作業者の安全を左右します。だからこそ、トルクレンチによる締め付けだけで満足するのではなく、軸力を「狙った値で・均一に・再現性高く」確保するための測定や確認作業が必要不可欠です。
【参考記事】京都大学研究情報リポジトリ
既設橋梁の高力ボルト残存軸力と軸力管理方法に関する研究
https://repository.kulib.kyoto-u.ac.jp/dspace/bitstream/2433/277357/5/dkogk05042.pdf
軸力管理するのに最適な工具は?
軸力管理を正確に行うために最適な工具は油圧式のボルトテンショナーです。この工具はボルトやナットを回転させるのではなく、ボルトの端部を油圧で引き上げることで、直接的に軸方向の張力、すなわち軸力を導入する仕組みとなっています。軸力を与えた状態でナットを手で締め付け、その後テンショナーの油圧を解放することで正確な軸力がボルトに残るという方法です。
この手法はトルクを利用する従来の締結方法と比較して、摩擦係数やトルク係数といった変動要素の影響をほとんど受けないため、極めて高い精度で軸力を管理できる点が特長です。たとえば風力発電のタワー基部や大型プラントの配管フランジの締結といった、ミスが許されない重要な接合部にはこのテンショナーが多く採用されています。
一方で作業効率やコストの面からはトルクレンチを使用する方法も一般的です。トルクレンチはナットに一定の回転力を与えることで締結を行う工具であり、現場作業者にとっては扱いやすく、導入コストも比較的低いため、日常的な保守や製造ラインで多く使用されています。ただし、この方法では軸力の導入に摩擦係数の影響が大きく関わるため、締結結果の軸力にばらつきが生じやすくなります。特に締結面やねじ部の潤滑状態、表面粗さなどの条件によって実際に得られる軸力が理論値から大きく外れることがあります。そのため、重要な部位では潤滑剤の種類や締結手順を厳密に管理し、トルク係数を補正した上で作業を行う必要があります。
【参考記事】科学技術情報発信・流通総合システム
油圧テンショナを用いたボルト締結体の軸力推定
https://www.jstage.jst.go.jp/article/hpi/54/4/54_170/_pdf
軸力と緩みの関係
ボルトの軸力と緩みには密接な関係があります。軸力よって接合部材同士が強く押し付けられ、摩擦力が生まれます。摩擦力は、ナットやボルトが外力や振動によって回転するのを防ぐ重要な役割を担っています。そのため、軸力が十分に確保されていれば、外部からの力や振動が加わっても、接合部は安定し、ボルトが緩む可能性は低くなります。
しかしながら、軸力が不足していると、部品同士の締結力が弱まり、摩擦力も小さくなります。この状態では、機械が稼働したときの振動や衝撃、あるいは熱による膨張・収縮といった繰り返しの負荷によって、ナットがわずかに回転し、次第に緩んでいく現象が起こります。これを「自己緩み」といい、特に回転体や高振動部では深刻な問題となります。
例えば、自動車のホイールナットが正しい軸力で締められていなかった場合、走行中の振動で徐々にナットが緩み、最終的にはホイールが外れるという重大事故につながる恐れがあります。また、配管のフランジ接合部においても、軸力が不十分であればガスケットの密着力が不足し、液体やガスの漏れが発生する危険性があります。
このように、軸力は目に見えないものですが、緩み防止の要であり、確実に管理しなければならない極めて重要な力です。単にボルトを締めればよいというものではなく、狙った軸力を確実に得るために、トルク管理や摩擦条件の確認、工具の精度点検など、あらゆる工程を通して適切な締め付けが行われることが求められます。
【参考記事】SpringerLink
ねじ締結具の緩みに関する研究のレビュー
https://link.springer.com/article/10.1007/s40544-021-0497-1
SpringerLinkとはシュプリンガー・ネイチャー社が出版する学術雑誌や書籍をオンラインで提供するプラットフォーム
摩擦係数が及ぼす軸力への影響
摩擦係数はボルト締結における軸力の大きさに直接的な影響を与える非常に重要な要素です。締め付け作業においては、一般的にトルクレンチなどを使って「トルク(ねじりの力)」をかけますが、そのトルクのすべてが軸力に変換されるわけではありません。実際には、トルクの多くは摩擦によって消費されてしまうため、摩擦係数が変わると、同じトルクをかけても得られる軸力が大きく変化するのです。
具体的には、ボルトのネジ部とナットの接触面、そしてナットと部材の座面には摩擦が発生します。この摩擦は、ボルトを回すときの抵抗として働き、トルクの約90%前後を消費します。残りの10%前後が、ようやくボルトを引っ張る力、つまり軸力に変わります。したがって、摩擦が大きければ大きいほど、軸力として伝わる力は小さくなり、逆に摩擦が小さければ、同じトルクでもより多くの力が軸力に変換されるという関係になります。
例えば、乾いたボルトや錆びたボルトを締める場合、摩擦係数が高くなります。このような条件では、同じトルクで締めても摩擦で力が逃げてしまい、軸力はあまり得られません。逆に、潤滑油を塗布した場合は摩擦係数が下がるため、同じトルクでもより多くの軸力が発生します。こうした違いは、製品の性能や安全性に大きく関わるため、摩擦条件を無視してトルクだけで締め付け作業を行うことは非常に危険です。
また、製造現場では、同じトルク値で締めても摩擦の変動によって軸力がバラバラになる「ばらつき現象」が問題になります。このため、設計段階で摩擦係数の管理値を設定したり、潤滑剤の使用条件を明確に定めるなどして、軸力の安定性を確保することが求められます。
【参考記事】ヤマハ発動機株式会社
ねじ締結と摩擦係数(2004-9 No.38 「コンポーネント技術」)
https://global.yamaha-motor.com/jp/design_technology/technical/feature/pdf/browse/38ts_03.pdf
軸力の求め方(基本的な考え方)
軸力は一般的に以下の式で求められます:
軸力(F) = トルク(T) ÷ トルク係数(k) ÷ ねじの呼び径(d)
トルク(T)
レンチなどでボルトを締めるときにかける「回す力」です。単位は N・m(ニュートン・メートル)です。
ねじの呼び径(d)
ボルトの太さのことです(たとえばM10ボルトなら直径は約10mm)。
トルク係数(k)
摩擦などを考慮した係数でだいたい 0.2 前後がよく使われます(ただし、ボルトの材質・潤滑状態などで変わります)。トルク係数は ボルトにどれくらいのトルクをかけたら、どれだけの軸力になるかを表す実用的な目安。摩擦の影響を含んだ経験則的な係数です。摩擦が大きければ、トルクを多くかけても軸力はあまり発生しませんので注意が必要です。
例:M10ボルトを30N・mで締めた場合の軸力
M10ボルト(直径10mm)を、トルク30N・mで締めた場合、トルク係数を0.2とすると:
つまり、このボルトには 約15,000ニュートン(15kN) の軸力がかかっている、ということになります。
実例:軸力の違いを比較
例えば、同じトルク30N・mでM10ボルトを締めても、「トルク係数」が違えば軸力が大きく変わります。
トルク係数k | 軸力F(N) |
---|---|
0.25 | 12,000 N |
0.2 | 15,000 N |
0.15 | 20,000 N |
0.1 | 30,000 N |
※潤滑ありと潤滑なしで2倍以上の差が出るのです。これは非常に重要なポイントです。
トルク係数の一般的な目安値
状態 | トルク係数(k)の目安 |
---|---|
ドライ(潤滑なし) | 約0.2〜0.25 |
潤滑あり(グリス使用) | 約0.1〜0.15 |
高潤滑(特殊処理) | 約0.08〜0.12 |
実際は試験で得られたトルク係数をご利用ください
軸力の測定方法
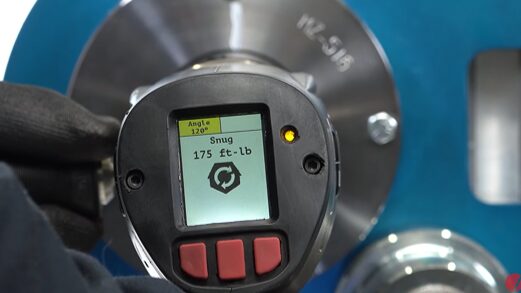
軸力計を使用した軸力測定
軸力の測定方法にはいくつかの手法がありますが、正確に軸力(ボルトやボルト締結体に発生する引張力)を測定するにはボルトの伸びや締結時の反力などを利用した方法が一般的です。以下に代表的な測定方法を説明します。測定目的によって適切な測定方法を選択するのが一般的でしょう。
超音波による軸力測定
もっとも高精度な方法のひとつが超音波パルス反射法です。ボルトの端から超音波パルスを送り、その反射時間を計測することでボルトの伸び=軸力を算出します。軸力とボルトの伸び量には明確な相関関係があるため、締結前後の超音波伝搬時間の差から、実際にかかっている軸力を非破壊で測定できます。
伸び計(ひずみゲージ)を使った測定
ボルトにひずみゲージ(ストレインゲージ)を取り付け、締め付けによるひずみから軸力を算出する方法です。この方法は比較的簡易で実験などにもよく使われますが、センサーの設置が必要であり、実機での使用には制限があります。精度も良好です。
軸力計を使った測定
軸力計とはボルトやナットの締結時に発生する軸方向の引張力、つまり「軸力」を正確に測定するための専用機器です。この装置はボルト締結の品質や信頼性を確保するうえで極めて重要な役割を果たしており、特にトルクだけでは締付けの正確性を保証できない場合に用いられます。
一般的な軸力計は模擬締結体、荷重検出部、そして表示ユニットの3つの要素から構成されています。まず模擬締結体は実際の構造体と似た環境でボルトを締め付けることができるよう設計された治具です。この中にボルトを挿入し、ナットで締め付けると、軸方向に引張力が発生します。
このとき使用されるロードセルには一般的なひずみゲージ式のほか、高応答性を持つ圧電式や、よりシンプルな構造の油圧式などがありますが測定精度と使いやすさのバランスから、実験や品質評価の場ではひずみゲージ式が最も多く使われています。また、表示ユニットには、リアルタイムで軸力を表示する機能や、記録・データ転送機能を持つものもあり、締付け条件の検証や工具性能の評価に用いられています。
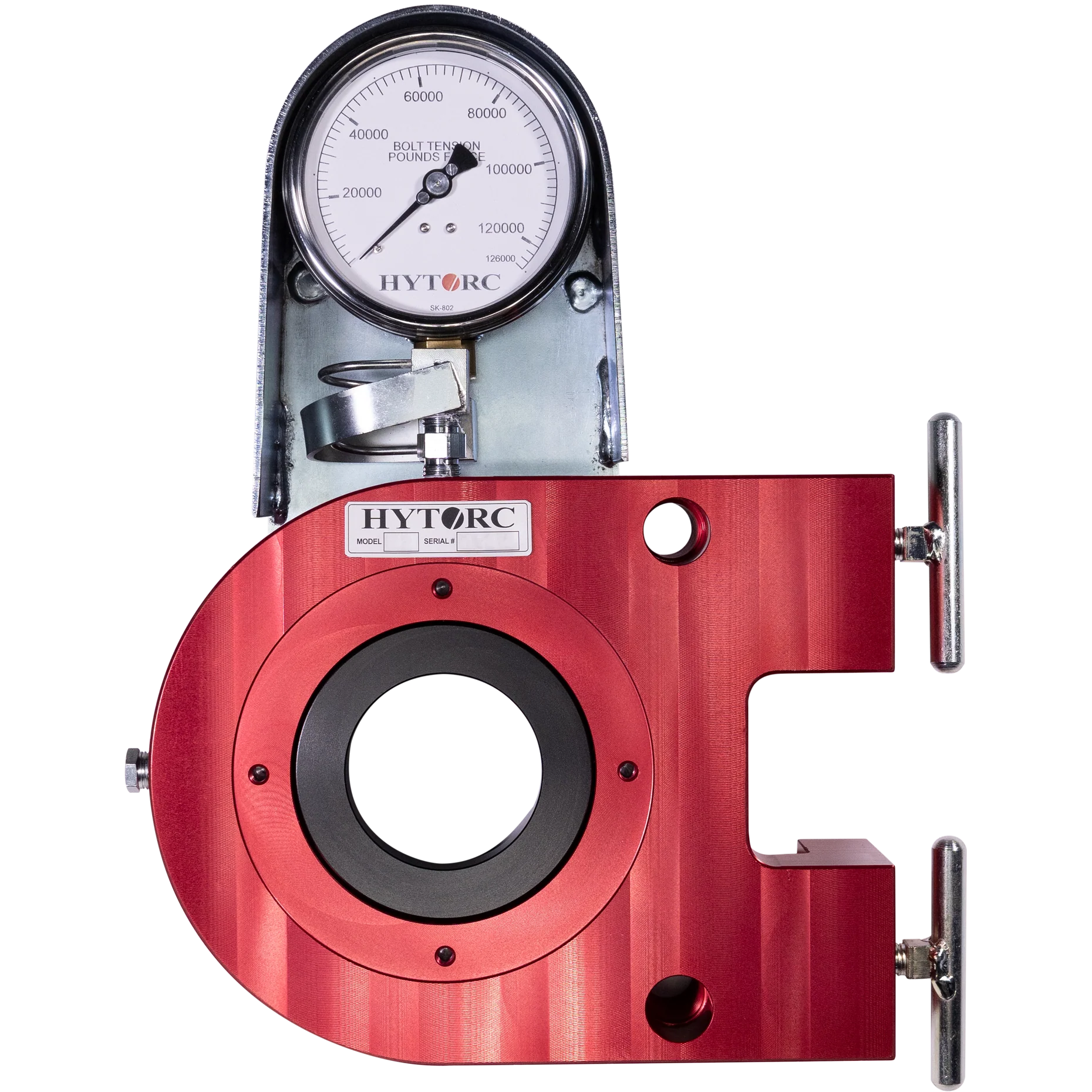
油圧式軸力計
軸力計の最大の利点は摩擦の影響を受けやすいトルク管理では見えにくい実際の締結力を直接的に、かつ高精度に測定できる点にあります。たとえば、潤滑剤の有無やネジ部・座面の状態によって軸力がどれだけ変動するかを実測できるため、設計の信頼性向上にもつながります。また、こうした測定結果は必要な締付けトルクを設定する際の基準データとしても活用されます。
ただし軸力計は現場での実締結に使われるものではなく、あくまで実験室や試験設備として位置付けられる機器です。現場での使用には不向きですが、その分だけ高精度な再現性と解析力を持っているため、製品の設計評価、工具の性能確認、または出荷前検査の場面で重宝される存在です。