トラックタイヤ交換を適切におこなうことは安全な運行のために非常に重要です。特に大型トラックやバスではホイールが大きく重量があるため、トラックタイヤ交換時のボルト締め付け作業を誤るとホイールの脱落やボルトの破損、トラックタイヤの偏摩耗などのトラブルにつながります。こうした問題を防ぐためには正しいトルク管理と締め付け手順を理解し、作業の精度を高めることが不可欠です。
【参考記事】国土交通省webサイト
大型車の車輪脱落事故防止「令和6年度緊急対策」
https://www.mlit.go.jp/jidosha/jidosha/tenkenseibi/images/kinkyu_taisaku.pdf
トラックタイヤ交換向けコードレス電動トルクレンチ
産業用ボルト締め付けソリューションのリーダーであるHYTORCは正確で信頼性の高い締め付けを容易にするために設計された様々な製品を提供しています。HYTORCのボルト締結工具、ファスナー、ソフトウェアを組み合わせることで危険なボルト締結作業の不具合を防ぐ事ができます。
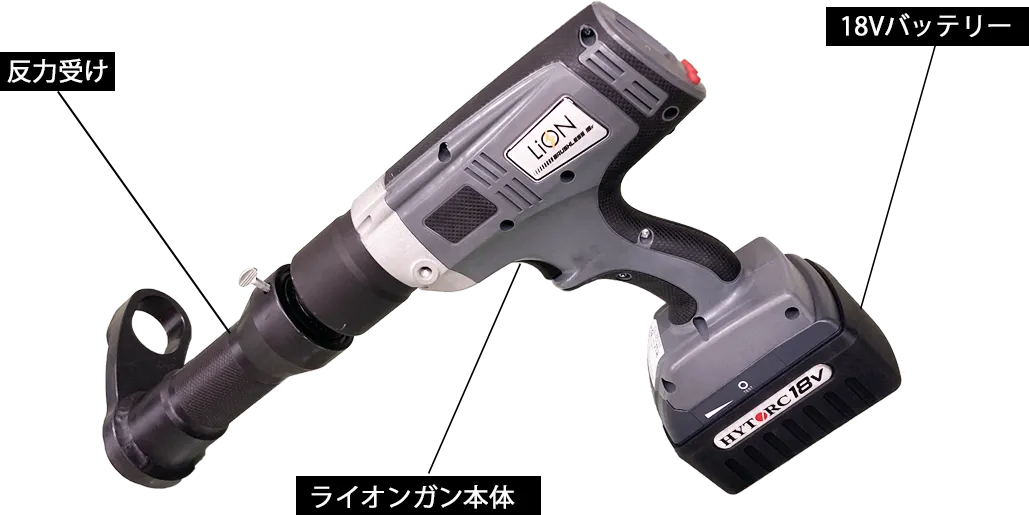
6.1kgの軽量設計で最大949Nmの高出力なコードレス電動トルクレンチ
トラックタイヤ交換向けコードレス電動トルクレンチライオンガン
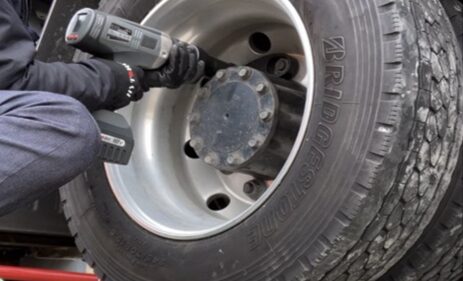
トラックタイヤ交換向けコードレス電動トルクレンチ
高度なトルク精度と携帯性を兼ね備えるHYTORCのコードレス電動トルクレンチライオンガンは正確なトルク管理を提供するバッテリー駆動のポータブルツールです。軽量で使いやすく設計されているため、トラックタイヤ交換に最適です。デジタル表示とプログラム可能なトルク設定により、ライオンガンは比類のないトルク精度を提供します。
この機能により、当て推量を排除し、トラックタイヤ交換時のボルトナットに正しいトルクを確実に与えることができるため、締め過ぎや締め不足のリスクを減らすことができます。この精度は車両コンポーネントの完全性を維持し、業界標準に準拠するために極めて重要です。
【参考記事】自動車業界WEBメディアレスポンス
インパクトレンチ? いえ200-6700Nmを制御できる電動トルクレンチ
ジャパントラックショー2022
https://response.jp/article/2022/05/15/357207.html
トラックタイヤ交換のトルク管理の品質とコンプライアンスの強化
HYTORCコネクトアプリをトラックタイヤ交換時に使用する事でメンテナンスチームはすべてのトルク管理を確実に記録し、電子的に保存することができます。このデータは業界の規制を遵守するために非常に貴重です。当社はメンテナンスチームがHYTORCツールを使いこなせるようになるためのトレーニングリソースとサポートを提供します。このトレーニングにより、技術者はトルク管理の重要性を理解し、ツールの効果的な使用方法を知ることができ、トラックタイヤ交換の全体的な品質と信頼性が向上します。
【参考記事】一般社団法人日本自動車タイヤ協会
大型トラックバスの車輪脱輪事故防止に向けて
https://www.jatma.or.jp/tyre_psd/safenews65.pdf
なぜトラックのタイヤ交換が必要なのか?
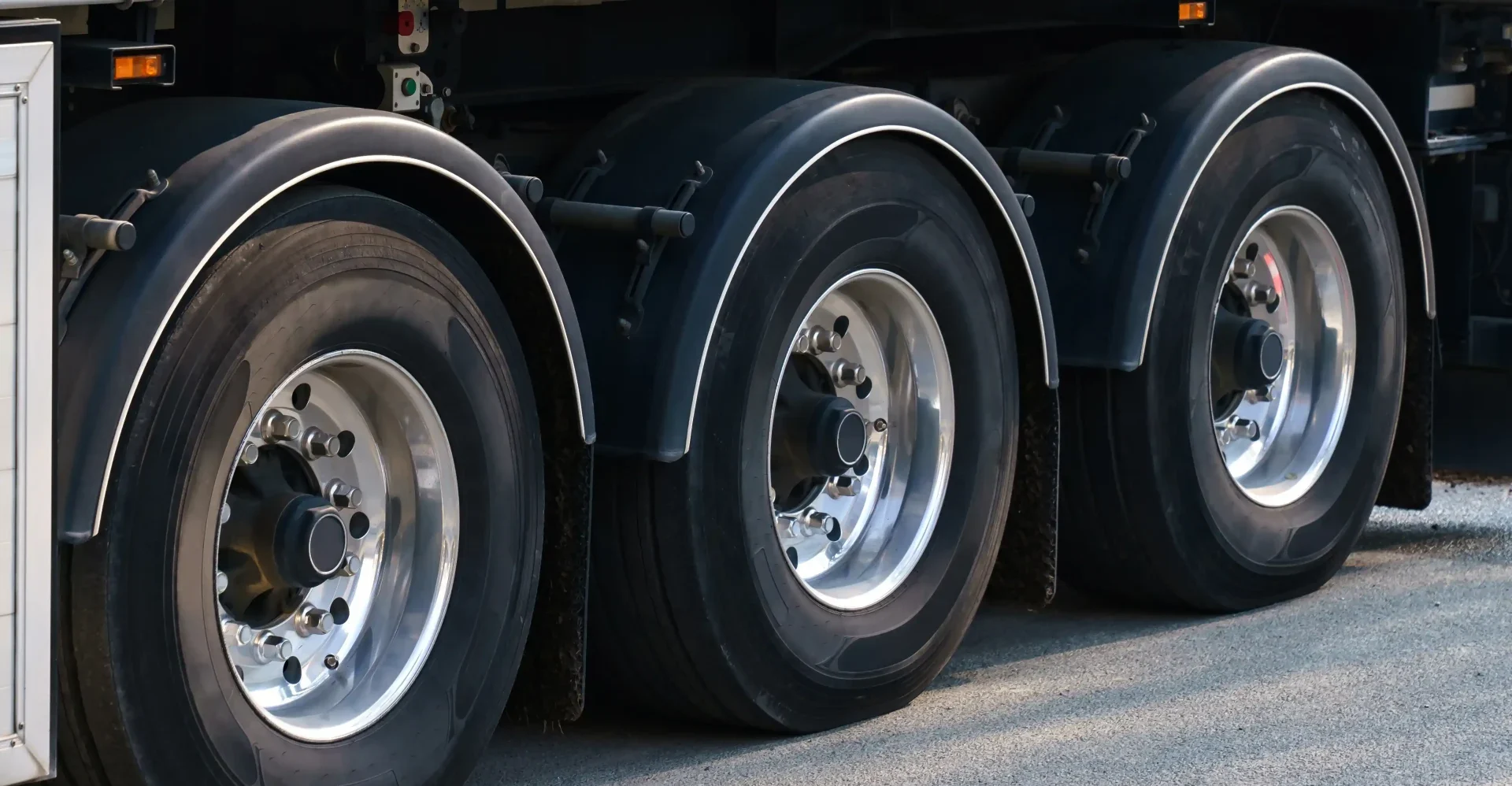
大型トラックのタイヤ
トラックのタイヤ交換が必要とされる最大の理由は安全性を確保するためです。タイヤは車両と路面をつなぐ唯一の接点であり、トラックが荷物を積んで走行する際、そのすべての重さを支えながら、走る、曲がる、止まるといった動きをコントロールする重要な役割を果たしています。もしこのタイヤの状態が悪くなれば、ブレーキをかけたときにしっかり止まれなかったり、雨の日に滑ったりといった危険が大きくなります。
また、タイヤは見た目が問題なさそうでも内部にダメージが蓄積していることがあります。特に長距離や高速道路を走るトラックではタイヤの空気圧や表面の劣化が原因で突然破裂する「バースト」が起きることがあります。バーストは非常に危険で高速走行中に起これば、車両がふらついたり、最悪の場合は横転や多重事故につながることもあるため、事前のタイヤ交換が欠かせません。
さらに劣化したタイヤを使い続けると燃費の悪化にもつながります。空気圧が適正でなかったり、摩耗してグリップ力が落ちていると、路面との抵抗が増えてエンジンに負担がかかり、余計に燃料を消費してしまいます。つまり、定期的にタイヤを交換することで、安全性だけでなく、経済的にもメリットがあるのです。
法律の面から見てもトラックのタイヤには厳しい基準があります。タイヤの溝の深さが1.6ミリ未満になると、整備不良と見なされ、違反点数や罰金の対象になることがあります。これは法的な問題であると同時に、明確な「危険サイン」でもあり、この状態に至る前に交換することが望ましいとされています。
【参考記事】シンク出版株式会社WEBサイト
冬用タイヤの残り溝点検を義務づけ─国土交通省
https://www.think-sp.com/2021/02/01/management-tire-check
トラックタイヤの交換時期
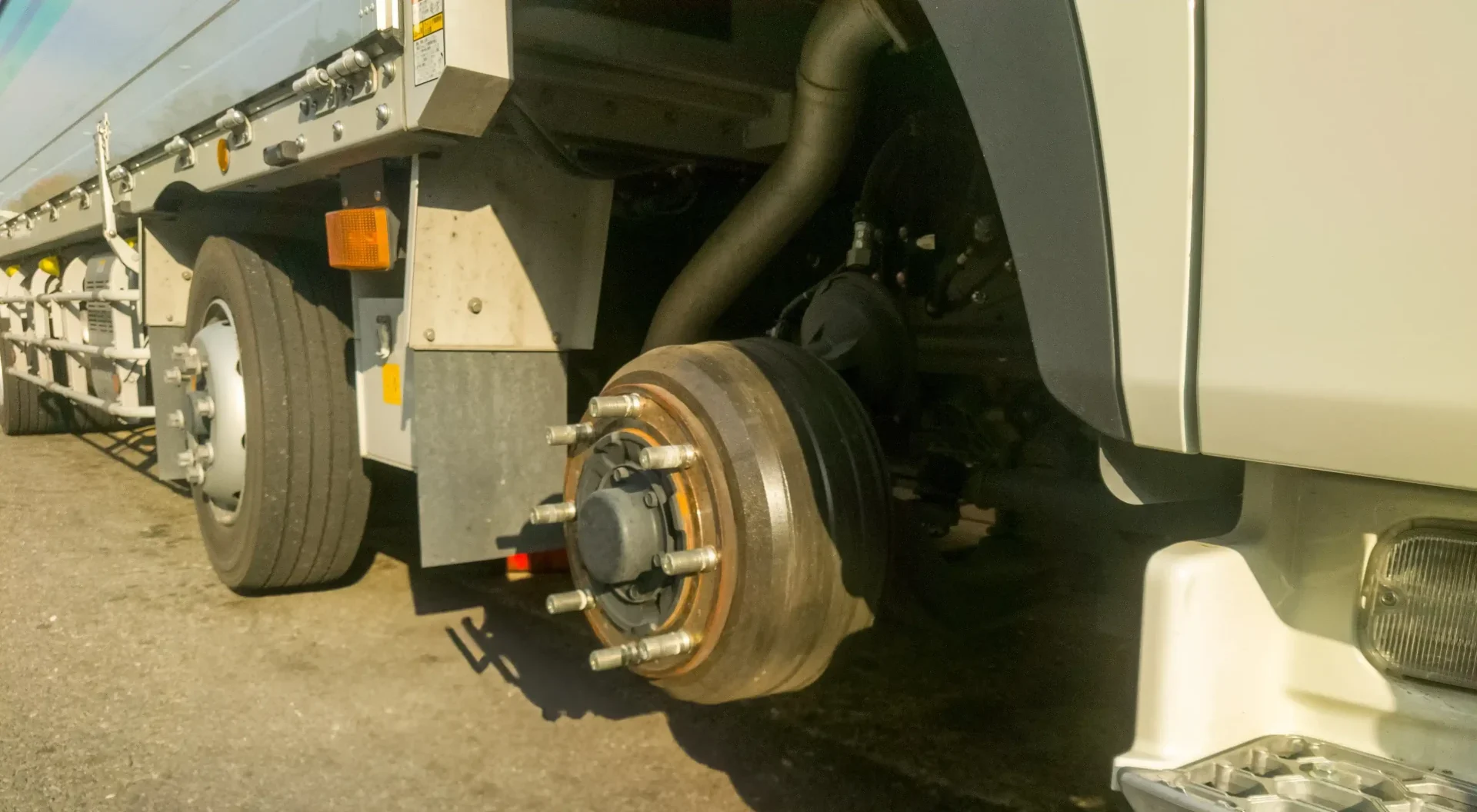
トラックタイヤ交換
トラックのタイヤ交換時期は使用環境や積載量、走行距離などによって変わりますがいくつかの具体的な基準があります。以下に、交換の目安となる代表的なポイントを詳しく説明します。
まず、最も分かりやすいトラックタイヤの交換時期の基準はタイヤの溝の深さです。日本の道路交通法ではタイヤの溝が1.6mm未満になると整備不良とされ、車検にも通らなくなります。タイヤの溝が浅くなると路面とのグリップ力が低下し、ブレーキを踏んでも止まりにくくなったり、雨天時にスリップしたりする危険性が高くなります。そのため、法律上の限界ギリギリまで使うのではなく、3~4mmを切ったあたりで交換を検討するのが現実的です。
次にタイヤの使用年数も重要です。タイヤのゴムは紫外線や気温の変化などで、時間の経過とともに劣化していきます。たとえ走行距離が少なくても、製造から4〜5年を経過したタイヤは劣化による亀裂や硬化が進んでいる可能性があるため、溝が残っていたとしても交換を考えるべきです。タイヤの側面には「製造年週」が刻印されているので、定期的に確認しておくとよいでしょう。
さらに、トラックの場合は走行距離も大きな判断材料になります。タイヤメーカーや運送業界の目安としては、おおよそ3万km〜5万km程度が交換の目安とされています。ただし、これはあくまで平均的な数字であり、重量物を積んで走るダンプや、長距離輸送を繰り返すトレーラーなどは、もっと早いタイミングでタイヤが摩耗することもあります。
また、溝の深さや年数、走行距離だけでなく、タイヤの外観の変化も重要なサインです。たとえば、サイドウォールにひび割れがあったり、変形やふくらみが見られた場合は、内部にダメージがある可能性が高く、バーストのリスクがあるため、早急な交換が必要になります。
以上のことから、トラックタイヤの交換時期は「○年経ったら」「○km走ったら」という一律のものではなく、溝の深さ・年数・走行距離・外観異常の4つを総合的に判断して決めることが大切です。日常点検でこれらの状態をチェックし、少しでも異常が見られた場合は、早めの交換を心がけることで、安全で安定した運行が可能になります。
【参考記事】公益社団法人全日本トラック協会
溝の深さによる交換基準(全日本トラック協会 ハンドブック)
https://jta.or.jp/wp-content/themes/jta_theme/pdf/anzen/kotsuanzen_ichiran/tenkenseibi_handbook202406.pdf
トラックタイヤ交換ボルト締め付け時の主なトラブルと対策
トラックタイヤ交換のボルト締め付けにおける主なトラブルの一つがホイールナットの緩みや脱落です。この問題が発生する原因としては、締め付けトルクが不足していることや、正しい締め付け順序が守られていないことが挙げられます。また、走行中の振動によってナットが緩むこともあるため、初回の締め付け後には50~100km走行した段階で増し締めを行うことが推奨されます。さらにナットの緩みを早期に発見できるように、マーキングを施し、視認性を向上させることも有効な対策となります。
トラックタイヤ交換時の過剰なトルクによるボルトの破断
一方でトラックタイヤ交換の締め付けトルクが過剰になりすぎると、ボルトが破断するリスクが高まります。特にエアーインパクトレンチを使用した際に規定値を超えて強く締め付けてしまうケースが多く、ボルトの摩耗やねじ山の損傷につながることがあります。そのため仮締めにはインパクトレンチを使用しても、本締めは必ずトルクレンチを使用し、メーカーが指定する適正なトルク値で締め付けることが重要です。また、ホイールボルトは繰り返しの締め付けで疲労が蓄積するため、定期的に点検し、摩耗やひび割れが見られる場合には早めに交換することが望ましいです。
ホイールの歪みやボルト穴の変形
ホイールの歪みやボルト穴の変形も締め付け作業において注意すべきポイントの一つです。これはボルトの締め付け順序を誤り、均等な圧力がかからないまま固定してしまうことで発生します。また、ホイールの取り付け面に異物が付着したまま締め付けると、ホイールが正しく密着せず、走行中に異常振動が発生することがあります。このような問題を防ぐためには締め付け作業の前にホイールハブとボルトの接触面を清掃し、異物やサビを取り除いてから締め付けることが重要です。さらに対角線順に均等な力で締めることでホイール全体が均等に固定され、歪みを防ぐことができます。
ホイールナットの締め付け不足による異常振動
トラックタイヤ交換時ホイールナットの締め付け不足による異常振動も走行時の安全性に大きく影響します。ナットがしっかりと締め付けられていないと、ホイールがわずかに動いてしまい、振動が発生することでさらに緩みが進行することがあります。また、ボルトの摩耗やねじ山の損傷が進んでいる場合には、適切なトルクで締め付けたつもりでも、実際には固定力が十分でないケースもあります。このようなトラブルを防ぐためには、初回の締め付け後に増し締めを行うとともに、定期的な点検を行い、ボルトやナットの状態を確認することが重要です。
トラックタイヤ交換時の推奨締め付けトルク
また、トラックタイヤ交換時の締め付けトルクの管理も非常に重要であり、一般的なトラックのホイールナットは600~700N・m前後のトルクで締め付けることが推奨されています。ただし、車種によって指定されるトルク値が異なるため、作業前に必ずメーカーのマニュアルを確認し、適正なトルクで締め付けることが必要です。締め付け作業は、仮締め、本締め、増し締めの3ステップで行い、最終的にはトルクレンチを使用して規定のトルクで締め付けることで、確実な固定を実現できます。
その他の注意点
ホイールナットやボルトの摩耗や劣化を見逃さないことも安全な運行を維持するうえで非常に重要です。ボルトやナットはトラックタイヤ交換のたびに繰り返し締め付けられるため、徐々に摩耗し、ねじ山が摩滅してしまうことがあります。こうした劣化を放置していると、たとえ適正なトルクで締め付けを行っても、十分な固定力が得られず、ホイールの緩みや脱落の原因となるリスクがあります。したがってナットやボルトの状態を丁寧に点検し、摩耗が見られる部品は早めに交換することが推奨されます。
また、取り付け面にサビや異物が付着していると締め付け力にムラが生じるため、ワイヤーブラシなどを使用して確実に清掃し、トラックタイヤ交換作業に入る前に万全の準備を整えることが求められます。視覚的な確認手段としてはナットに緩み防止マーカーを施す方法も効果的です。運行前点検の際にマーキングのずれを目視で確認できるため、トラックタイヤ交換後のナットの緩みを早期に発見することができます。
特にISO方式のトラックタイヤ交換では適正なトルク管理と締め付け順序を厳守することが不可欠です。不適切な作業手順はホイールの脱落やボルトの破損といった重大な事故につながる可能性があるため、日常的な点検と定期的な増し締めが非常に重要になります。正しい手順でトラックタイヤ交換を実施することで安全な運行を支えるだけでなく、ホイールやボルトの寿命延長にもつながるのです。
コンプライアンスと規格
業界規制への対応 運輸業界には厳しい規制や規格があり、その多くは車両部品に特定のトルク要件を義務付けています。制御されたトルクを確保する事で商用車がこれらの規制を遵守し、潜在的な罰金や法的問題を回避することができます。
管理されたトルクは車両メンテナンスに一貫したアプローチを提供します。校正されたトルクツールを使用し、指定されたトルク値に従う事でメンテナンスチームは各ファスナーを毎回同じ基準で締め付けることができます。この一貫性により車両の全体的な信頼性と効率が向上します。
【参考記事】神奈川県貨物自動車運送適正化事業実施機関
「タイヤ脱着作業を実施した車両は50~100km走行後にホイールナットの増し締めを運転者または整備要員に実施させる」
https://www.kana-tekisei.jp/info/laws/2394/
トラックタイヤにおけるISOとは?
トラックタイヤにおけるISOとは国際標準化機構(ISO)が定める世界共通の技術基準のことを指します。この規格はタイヤやホイールの寸法、安全性能、表示方法、試験方法など多岐にわたる項目を統一することで国やメーカーの垣根を越えてタイヤの品質と安全性を確保することを目的としています。ISOの規格に準拠することで製品の互換性が確保され、整備や交換作業の効率も高まります。トラックのような大型車両ではタイヤにかかる負荷や使用条件が非常に過酷であるため、こうした国際規格に従うことは、事故の防止、燃費の向上、部品の長寿命化といった面でも大きな意義を持っているのです。
【参考記事】一般社団法人日本自動車工業会
新ISO方式ホイール取扱いガイド
https://www.jama.or.jp/operation/truck-bus/docs/Wheel.compressed.pdf
トラックホイールにおけるJISからISOへの移行の理由
かつて日本国内ではトラックのホイール設計や製造にはJIS規格が使われていました。これは日本国内の車両設計、製造、整備、流通などに適した仕様として機能しており、国内トラック市場においては問題のない体制が築かれていました。
しかし、時代とともにトラック業界を取り巻く環境は大きく変化しました。とくに2000年代以降、トラックの製造・流通・メンテナンスが国際的なサプライチェーンの中で行われるようになり、JISだけでは対応しきれないケースが増えてきたのです。
具体的には、日本国内で使用されるトラックであっても、ホイールの製造拠点がアジア諸国やヨーロッパであったり、輸送される貨物が国際間をまたいだりするようになりました。その中で、JIS規格のホイールとISO規格のホイールにわずかな寸法の違いがあるため、互換性の問題や整備時の不一致、事故リスクなどが表面化してきました。
とくに注目すべきは、ホイールのボルト穴の寸法やナットの角度の違いです。JIS規格では、ナット座面が60度のテーパー角で設計されているのに対し、ISOでは通常、90度の球面座(スフェリカル)が主流です。この差異により、本来は一致すべきハブとホイールの接合部にわずかな“浮き”や“ズレ”が生じ、適正にトルクをかけても脱輪事故などのリスクが高まる恐れが指摘されてきました。
こうした背景から、日本国内の車両メーカーや部品サプライヤーも、国際的な整備性と安全性の確保を最優先に考え、ISO規格を採用する動きが加速しています。実際、日野自動車、いすゞ自動車、三菱ふそう、UDトラックスといった大手商用車メーカーも、現在は新型車両についてはISO方式のホイールを標準装備とし、JIS方式は旧車両・一部用途に限定されるようになってきています。
【参考記事】日刊自動車新聞電子版
商用車4社、4トン級以上の車輪をISO方式に切り替え
https://www.netdenjd.com/articles/-/24215
なぜISO方式のホイールが有利なのか?
ISO方式のホイールは世界各国で広く採用されており、トレーラーや大型トラックの分野で特に主流となっています。ISO規格に統一することで整備士が海外製の車両・部品に対応しやすくなり、部品の調達も円滑になるという実利的な利点があります。また、ホイールの取り付け時のトルク管理もISO方式のほうが座面の安定性が高いため、締結の信頼性が向上するとされています。脱輪事故のリスクが社会問題となっている日本国内でもこうした面からISO方式の導入が推進されているのです。このようにトラックホイールにおけるJISからISOへの移行は、「安全性の確保」「国際的な互換性の追求」「整備現場でのトラブル防止」といった非常に実務的な課題を解決するための合理的な判断と言えます。
締め付けトルクの設定・管理がよりシビア
ISOホイールは設計上のトルク許容範囲が比較的狭いため、指定されたトルク値を正確に守る必要があります。一方でJIS方式はある程度の誤差を吸収しやすい設計のため、トルク管理が多少ラフでも問題が起こりにくい傾向がありました。そのためISO方式に変えた際に従来と同じ感覚でインパクトレンチを使用すると締め過ぎや締め不足が発生し、結果としてホイールナットが緩むという事例が発生してしまいます。
【参考記事】ベストカーWeb
やはりISO方式が原因なのか!?10年で10倍増加!頻発する大型トラックのタイヤ脱輪事故の深層
https://bestcarweb.jp/feature/column/444346
使用条件によっては座面のなじみ不足が発生する
新しいISOホイールやナットでは座面同士がなじんでいないため、初期なじみが起きやすいという現象があります。これはJIS方式でも起こりうる現象ですがISOの球面座ではより顕著になることがあります。そのためホイール交換後の増し締めが特に重要です。
【参考記事】米国インターモーダル業界団体
Webb Torque Specification Guidelines
座面のなじみ不足によるトルク低下を防ぐため、再トルクが推奨されております
https://intermodal.org/documents/WebbWheel-WebbTorqueSpecificationGuidelines.pdf
トラックタイヤ交換作業の効率化は市場から求められています
トラックのタイヤ交換に時間がかかります。普通車に比べて作業の規模が大きく、安全確認にも非常に気を遣う必要があるからです。まず、トラックのタイヤはとても大きくて重く、1本だけでも50〜80キロ、ホイールを含めると100キロを超えることもあります。そのため、人の手だけでは扱えず、専用のリフトや機械を使って慎重に作業しなければなりません。
さらに、ホイールを固定しているナットの数も多く、大型トラックでは1輪に10個前後のナットが使われています。それぞれが600Nm以上の力で締め付けられているため、これを外すのにも時間がかかりますし、締め直す際には適切なトルクで締める必要があります。ここをいい加減にすると、走行中にタイヤが外れるなどの重大な事故につながる可能性があるため、慎重に作業を進める必要があるのです。
また、タイヤそのものをホイールから取り外して新しいものと交換する「組み換え作業」も、トラック用の硬くて分厚いタイヤでは特に大変です。専用のタイヤチェンジャーを使っても手間がかかり、時間も余計に必要になります。加えて、大型トラックはタイヤの本数が多く、後輪がダブルになっている車両では1つの位置に2本ずつタイヤが装着されているため、作業量も倍になります。
これに加えて、すべてのタイヤに対して空気圧の確認や、ナットの増し締め、安全確認を丁寧に行う必要があるため、結果的に1本や2本の交換でもかなりの時間がかかることになります。このように、トラックのタイヤ交換は「重い」「本数が多い」「作業が複雑」「安全確認が必須」といった理由から、どうしても時間がかかってしまうのです。作業する人たちは、スピードよりも確実さと安全を優先する必要があります。
【参考記事】グローバル動向:市場成長が示す需要の高まり
トラックタイヤチェンジャー市場の展望、機会、競争力の洞察
https://www.linkedin.com/pulse/truck-tire-changer-market-outlook-opportunities-competitive-ynftc/
結論
トルク管理はトラックタイヤ交換作業において重要な側面であり、安全性、性能、業界標準への準拠を保証します。コードレス電動トルクレンチであるライオンガン、GRIP-TIGHT™ NUT、およびConnect Appは正確で信頼性の高いトルク管理を実現するための強力なボルト締結工具です。これらの製品をメンテナンスに組み込むことで商用車の信頼性、効率性、安全性を向上させ、投資を保護し、スムーズな運用を実現する事ができます。まずは一度このトラックタイヤ交換向け工具をご試用下さい。