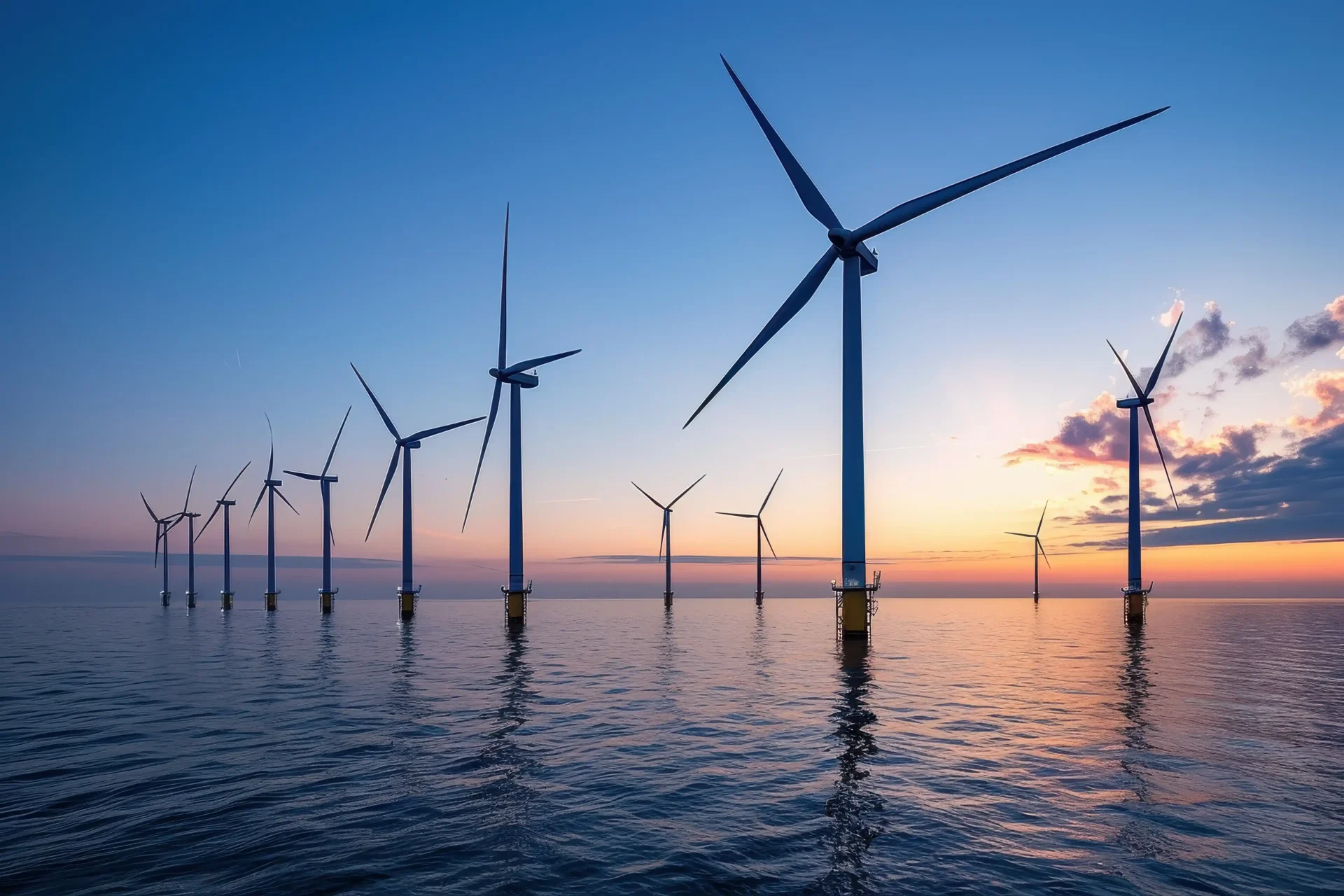
洋上風力発電
このマーケットは急速に成長しており、特に欧州や中国が市場をリードしています。このページでは洋上風力発電の種類や風車メーカーや特徴について解説します。特に日本では沿岸部の水深が深いため、浮体式の導入がカギを握るとされています。
洋上風力発電の風車メーカーについて
まず、洋上風力発電の風車メーカーは世界的にいくつかの大手企業が市場をリードしており、それぞれ独自の技術や戦略を持っています。特にヨーロッパの企業がこの分野を先行しており、近年ではアメリカ企業も市場参入を進めています。
GE Vernova
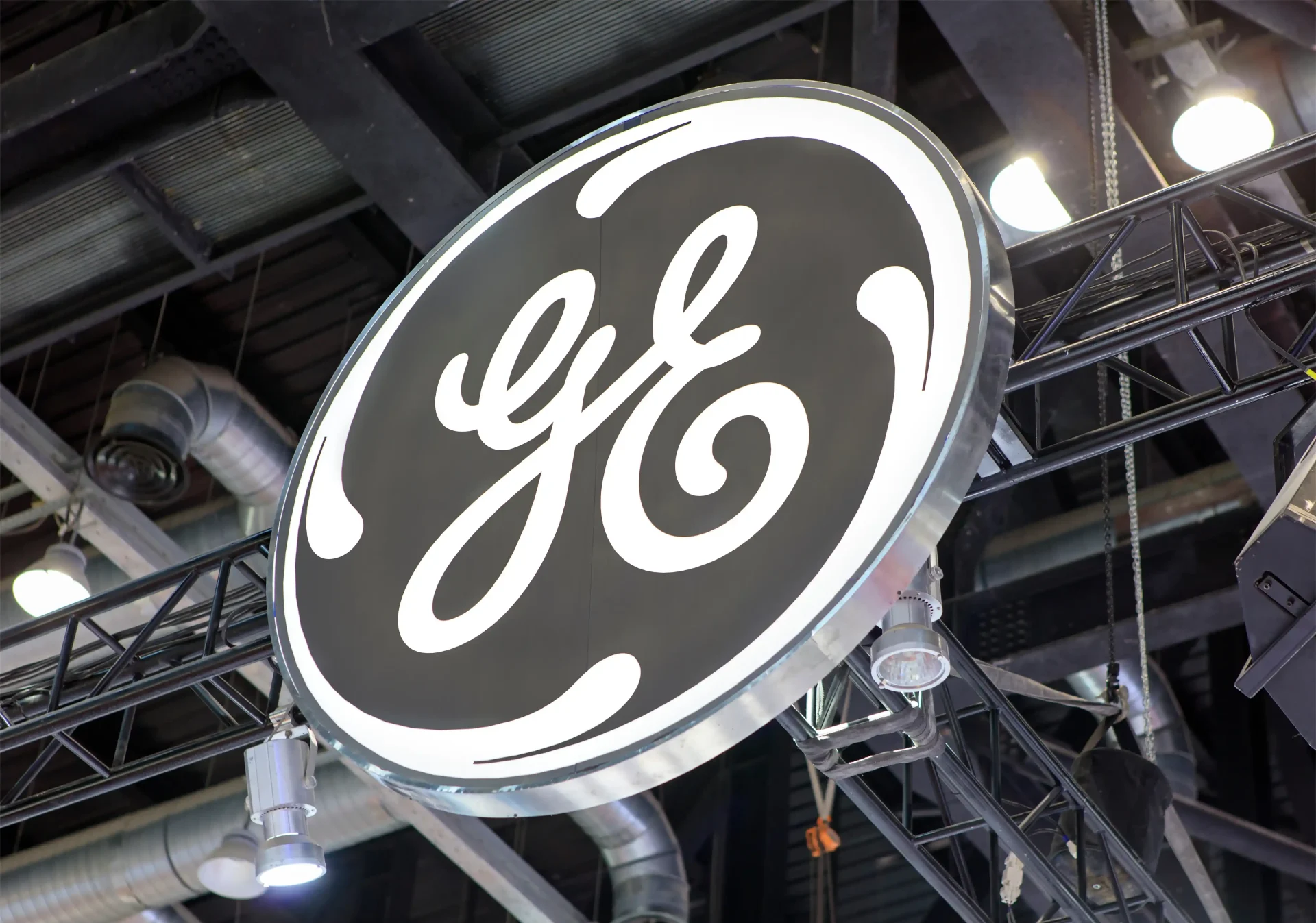
GE Vernova社
GE Vernovaはアメリカのゼネラル・エレクトリック(GE)から分社化されたエネルギー関連事業を専門とする企業です。GEは長年にわたり、航空、医療、エネルギーなど多岐にわたる分野で事業を展開してきましたが2021年に企業の再編を発表し、それぞれの分野を独立させる決定をしました。その結果、エネルギー事業を担うGE Vernovaが誕生し、2024年4月に正式にGEから分離しました。
GE Vernovaの事業領域は、風力発電(陸上・洋上)、ガスタービンを用いた発電技術、電力の送配電システム、水力発電、さらには水素や原子力を活用したエネルギーソリューションなど、多岐にわたります。これらの技術を通じて、持続可能なエネルギーの供給を目指し、カーボンニュートラル社会の実現に貢献することを企業のミッションとしています。
ヴェスタス・ウインド・システムズ
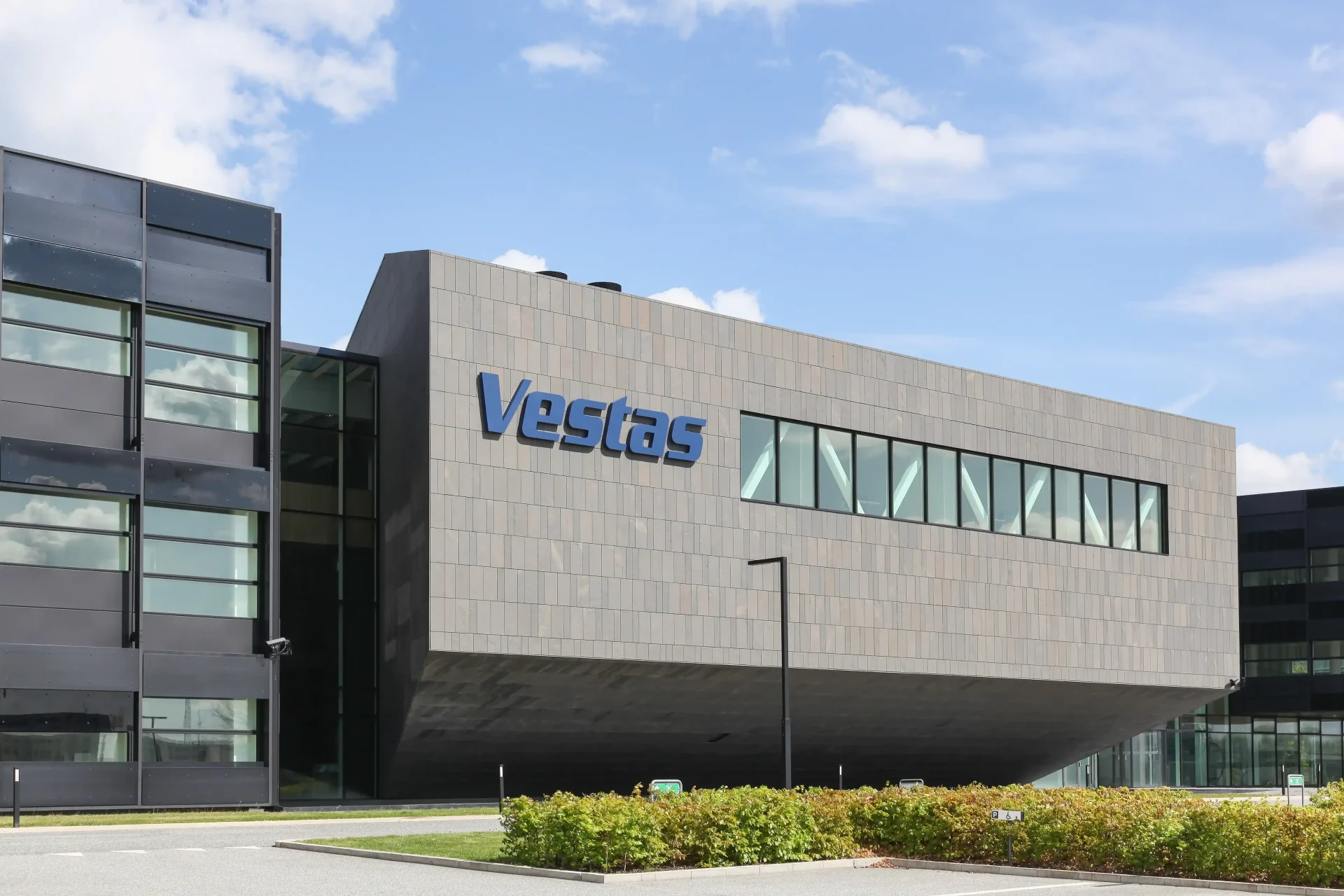
ヴェスタス社
次にデンマークのヴェスタス・ウインド・システムズ(Vestas Wind Systems)は洋上風力発電分野でシーメンス・ガメサに次ぐ世界第2位のメーカーです。ヴェスタスはもともと陸上風力発電の分野で強みを持つ企業でしたが近年では洋上風力発電にも注力し、大型風車の開発を進めています。特に直径236メートルの巨大なローターを持つ「V236-15.0 MW」という最新の洋上風車を開発し、15MWクラスの高出力風車市場に参入しました。ヴェスタスはスコットランドの「Seagreen」やドイツの「Baltic Eagle」など、ヨーロッパの主要な洋上風力プロジェクトに採用されており、アジア市場にも展開を広げています。
シーメンス・ガメサ・リニューアブル・エナジー
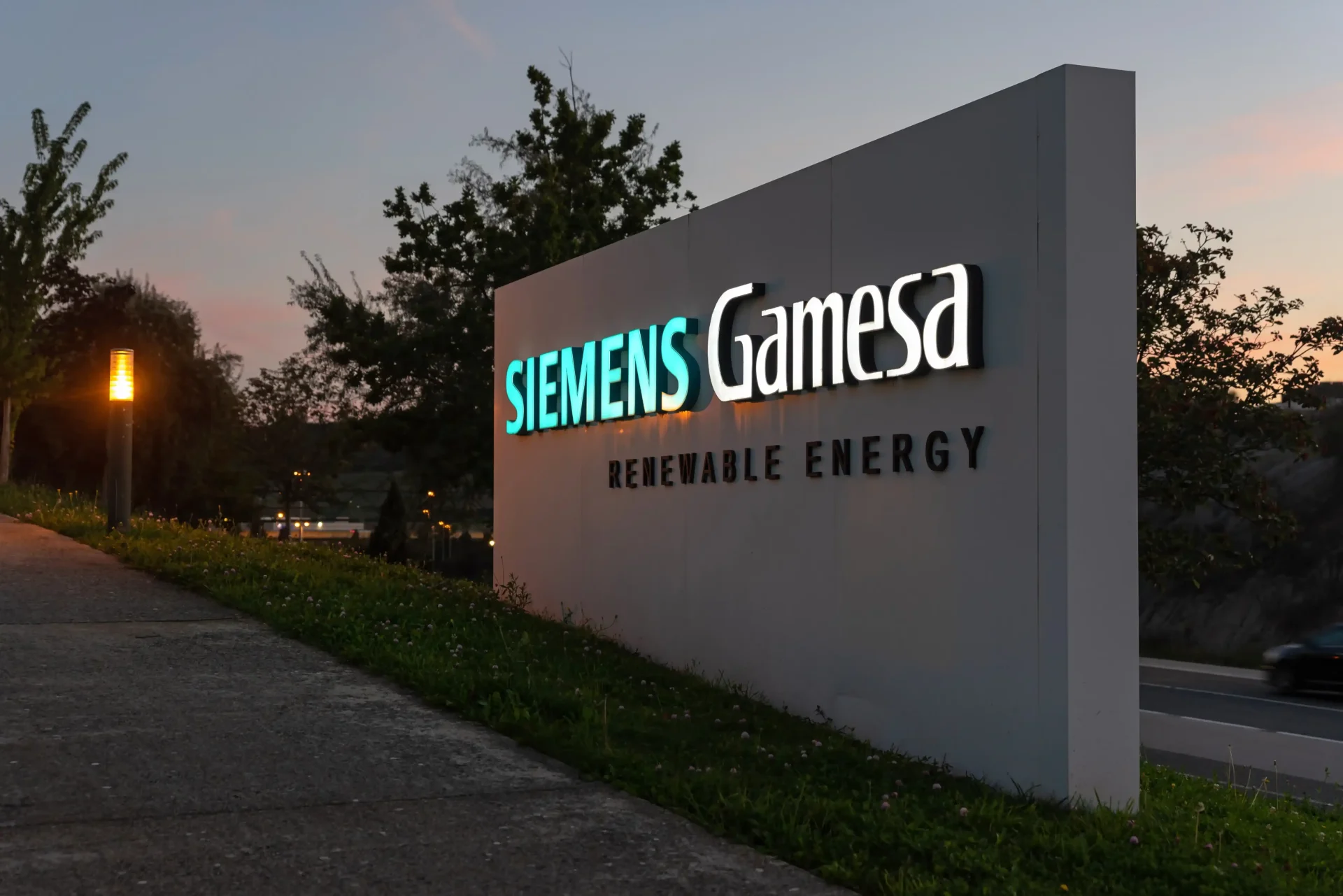
シーメンス・ガメサ
世界最大のシェアを持つのがシーメンス・ガメサ・リニューアブル・エナジー(Siemens Gamesa Renewable Energy)です。この会社はドイツのシーメンスとスペインのガメサが合併して誕生した風力発電分野のリーディングカンパニーであり、特に洋上風力発電市場では圧倒的なシェアを誇ります。シーメンス・ガメサの風車はギアボックスを使わない「ダイレクトドライブ技術」を採用することでメンテナンスの負担を軽減し、より長期間にわたって安定した発電を可能にしています。また、イギリスのHornsea 2やオランダのBorsseleなど世界最大級の洋上風力発電プロジェクトに風車を提供しており、アジア市場にも積極的に進出しています。
洋上風力発電の風車の大型化が主流になっている理由
近年、洋上風車の大型化が急速に進んでおり、現在では15MW級の風車が開発導入されるなど技術革新が続いています。例えばシーメンス・ガメサの「SG 15-236 DD」やGEの「Haliade-X 15MW」、ヴェスタスの「V236-15.0 MW」など、ローター直径が200mを超える巨大な風車が次々と登場しています。ではなぜ洋上風車は大型化が主流になっているのでしょうか。その理由を詳しく説明します。
発電効率の向上とコスト削減
洋上風力発電では、1基の風車が大きくなるほど発電量が増え、同じ設備投資でもより多くの電力を生み出せるというメリットがあります。風車の発電量は、ブレードが通過する面積(ローターの回転面積)に比例するため、ブレードを長くすればするほど、より多くの風を受けて発電できるようになります。例えば、ローター直径が2倍になれば、発電能力は約4倍に増えるため、同じ面積の海域でより多くの電力を生産できるのです。
また、大型風車を導入することで1MWあたりの建設コストを削減できるという経済的なメリットもあります。洋上風力発電の建設には大型のクレーン船や作業船、海底基礎の設置など多額のコストがかかりますが風車の台数を減らせば、全体の建設コストを抑えることができます。例えば10MW級の風車を10基設置するよりも15MW級の風車を7基設置する方が同じ発電量を確保しつつ、施工や維持管理のコストを削減できるのです。
洋上の広大なスペースを活用できる
陸上風力発電では土地の確保が課題となり、大型風車の設置が難しい場合があります。しかし洋上では広い海域を活用できるため、ブレードが長くても周囲の障害物に影響されにくく、スペースの制約が少なくなります。特に深海に対応できる浮体式洋上風車の技術が進展することで今後はさらに大型の風車が導入される可能性があります。
さらに洋上は陸上よりも平均風速が高く、安定した風が吹くため、大型風車の特性を最大限に活かすことができます。ブレードが長くなることで、より高い位置の風を捕えることができ、発電効率の向上につながります。
メンテナンスの効率化
洋上風車のメンテナンスには多くのコストがかかります。陸上風車であれば、簡単にアクセスできるため定期点検や修理が比較的容易ですが、洋上風車の場合、点検や修理のために作業船や特殊な設備が必要となり、それに伴う人件費や燃料費などの運用コストが高くなります。そのため、大型風車を導入することで風車の数を減らし、メンテナンスの負担を軽減することができます。
また、最近では、リモートモニタリング技術やAIを活用した自動点検システムが導入され、大型風車の管理がより効率的になっています。例えば、風車にセンサーを搭載し、ブレードや発電機の状態を常時監視することで、故障の予兆を早期に検知し、計画的なメンテナンスを行うことが可能です。
風車の台数を減らし、環境への影響を抑える
洋上風力発電は再生可能エネルギーとして環境に優しいとされていますが、それでも設置する際には、海洋生態系や漁業への影響が懸念されることがあります。特に、風車の台数が増えると、それだけ海底に基礎を設置する必要があり、施工時の騒音や振動が海洋生物に影響を及ぼす可能性があります。
しかし、大型風車を導入することで、発電量を維持しながら風車の台数を減らすことができるため、環境負荷を最小限に抑えることができます。例えば、100基の5MW風車を設置する代わりに、50基の10MW風車を設置すれば、同じ発電量を確保しつつ、環境への影響を半減させることができます。
技術革新による洋上風力発電大型化の実現
近年の技術革新により、大型風車の設計や製造がより効率的になってきました。特に軽量かつ高強度なカーボンファイバーや複合材料を使用することで、ブレードのサイズを大きくしながらも耐久性を向上させることが可能になりました。また、「ダイレクトドライブ方式」の採用によって、ギアボックスのメンテナンスが不要になり、風車の大型化を後押ししています。
さらに、大型風車の設置技術も進化しており、大型クレーン船や特殊な輸送船が開発されたことで、より大きな風車を効率的に海上へ運搬・設置できるようになっています。これにより、従来の技術では設置が難しかった15MWクラスの風車が実用化されつつあります。
洋上風力発電の種類について
洋上風力発電には、大きく分けて「着床式」と「浮体式」の2つの方式があります。それぞれの方式は、設置場所の水深や環境条件によって適したものが異なり、メリット・デメリットも違います。ここでは、それぞれの特徴について詳しく説明します。
着床式(固定式)洋上風力発電
着床式洋上風力発電は風車の基礎を海底にしっかりと固定する方式です。この方式は水深が比較的浅い海域(50メートル未満)に適しており、現在の洋上風力発電の主流となっています。着床式の中にも基礎の設計によっていくつかの種類があります。
最も一般的なのが「モノパイル基礎」という方式です。これは大型の鋼管を海底に打ち込んで固定するシンプルな構造で、設置コストが比較的低く、施工も容易なため、世界中で広く採用されています。しかし海底の地質によっては適用できない場合があり、水深が深くなると強度の確保が難しくなります。
次に、「ジャケット基礎」と呼ばれる方式があります。これは、鉄骨フレームを組んだような構造で、モノパイル基礎よりも安定性が高く、水深50メートル程度までの比較的深い海域でも利用できます。特に北海など、海洋環境が厳しい地域でよく使われています。
また、「重力式基礎」という方式もあります。これは、コンクリートや鋼鉄で作られた大型の基礎を海底に設置し、その重さによって安定させる方式です。この方式は海底を掘削する必要がなく、環境負荷が少ないという利点がありますが、基礎自体が大きく重いため、輸送や設置のコストが高くなりがちです。
着床式の洋上風力発電は、技術が確立されており、コスト面でも比較的安価で済むため、多くの国で採用されています。しかし、設置できる場所が水深の浅い沿岸部に限られるという制約があります。そのため、水深の深い地域でも利用できる技術として、「浮体式」の開発が進められています。
浮体式(フローティング式)洋上風力発電
浮体式洋上風力発電は、風車を海底に固定せず、浮かせた状態で設置する方式です。この方式の最大の利点は、水深が深い場所でも設置できることです。日本の沿岸部は急に深くなる地形が多いため、特に日本に適した技術として注目されています。
浮体式にもいくつかの種類があります。最も一般的なのは「セミサブ式」と呼ばれる方式で、複数の浮体を連結して安定させる構造になっています。この方式は比較的シンプルで導入しやすく、すでにノルウェーの「Hywind」プロジェクトなどで実用化が進められています。
また、「スパー式」という方式もあります。これは、風車の下に長い円筒形の構造物を海中に沈めることで安定させる仕組みになっています。スパー式は重心が低く安定性が高いのが特徴ですが、海底までの深さが必要なため、設置場所が限られます。
さらに、「テンション・レッグ・プラットフォーム(TLP)式」という方式もあります。これは、海底にアンカーを設置し、張力をかけて風車を固定する方法です。この方式は浮体が大きく揺れにくいため発電効率が高くなりますが、設計や施工の難易度が高く、現在のところ実用化が進んでいる例は少ないです。
浮体式の洋上風力発電は、深海でも設置できるという大きなメリットがありますが、まだ技術開発の途中であり、コストが高いという課題があります。特に、風車を安定させる技術や、メンテナンスを効率的に行うための仕組みが今後の重要な研究課題とされています。
どちらの方式が主流なのか?
現在のところ、世界の洋上風力発電は着床式が主流です。これは技術が確立されており、コストが比較的低く抑えられるためです。しかし、今後は浮体式の技術開発が進み、深海にも設置できる風力発電が増えていくと考えられています。
洋上風力発電には「着床式」と「浮体式」の2つの方式があります。着床式は現在の主流でコストが低く安定した技術ですが水深の浅い場所にしか設置できません。一方、浮体式は深海でも設置可能で日本の地形には適していますがまだ技術開発の途中であり、コストが高いという課題があります。今後の技術革新によって、浮体式がより一般的になる可能性が高く、洋上風力発電の発展に大きく貢献すると期待されています。
方式 | 設置場所 | メリット | デメリット |
---|---|---|---|
着床式 | 水深50m未満 | コストが安い、技術が確立 | 水深が深い場所では設置できない |
浮体式 | 水深50m以上 | 深海でも設置可能 | 技術開発中、コストが高い |
風力タービンの安定性と運用の安全性を高めるためのボルト締結
風車タワーの建設では安定性が中心的な役割を果たします。というのも風車が大型化するほど構造物に作用するてこ力も大きくなるからです。風車メーカーのエンジニアは出力が増加し、ハブの高さが増加しているにもかかわらず、力を基礎に安全に誘導するという特別な課題に直面しています。洋上風車の場合ボルトサイズはM56、M64、M72 が標準であることがよくあります。HYTORC はこれらのボルト締結を最適化する方法と全体的に設計を改善する方法を調査しました。産業用ネジ締めの専門家はコストのプレッシャーも念頭に置いていました。あらゆる改善は関係者全員にとってコスト面でのメリットが得られる場合にのみ実行される可能性があるからです。
ボルトの位置と数は風力タービンの安定性にとって非常に重要です。有利な解決策は動力伝達を最適化するためにそれらをできるだけ外壁に近づけることです。新しい、より大きなピッチ円上に、より多くの接続要素を配置することが可能となり、より高い全体的な予荷重力で配置することができます。したがって、外部から作用する力はより多くのボルトに分散され、個々の接続要素にかかる負荷が軽減されることになります。
安全、迅速、少ない労力で設置できます
これまではクレーンを使用して数トンのセグメントを正確に取り付けるために、ゆるく挿入されたネジが使用されていました。ねじ締めの際にフィッターが重い工具を下から持つ必要がないように、ねじをフランジから抜き、下から再度挿入することで、上からねじ込むことができるようになります。面倒で肉体的に負担のかかる作業は、半自動組立トロリーを使用すれば不要になります。必要な工具をしっかりとクランプして、フランジのネジ接続を下から安全に、ほとんど力を入れずに次々と締めることができます。工具の移動も含めてネジ締め作業にかかる時間は約60秒です。フランジは、約 120 個のネジ セットと 2 台の組立トロリーを使用して、1 時間でネジ締めできます。利点: 組み立てが大幅に短縮され、タワーごとのクレーン時間が大幅に短縮され、組み立てチームの身体的負担が軽減されて労働安全性が大幅に向上します。
HYTORCのトルクレンチを使用したボルト締結は長期的に運転、サービス、メンテナンスのコストを削減します。シームレスなデータ管理システムにより、コストのかかる検査が不要になり、メンテナンス間隔も延長できます。油圧降伏点制御締付(SGA)などのHYTORCの革新的な締付方法により、風力タービンの資源効率の高い軽量構造も最適にサポートされます。
タワーボルトの再考:トロリーシステム
HYTORCトロリーセットは油圧タワーのボルト締め用の半自動組立トロリーです。技術者の負担を軽減し、組立時間やクレーン作業時間を短縮します。